3D Printers/Ender 5 plus: Difference between revisions
No edit summary |
|||
(102 intermediate revisions by 3 users not shown) | |||
Line 1: | Line 1: | ||
[[File: | [[File:Ender_5_plus.jpg|thumb|300px|Ender 5 Plus]] | ||
== Status == | == Status == | ||
<onlyinclude> | <onlyinclude> | ||
* ''' | * '''Working - Read wiki instructions before use''' | ||
* | * You must download the configs in the "Config" section below. | ||
* ''' | **The printer should be "set and forget", the touch probe and the bed mesh should give perfect first layers everytime. Still wipe the build plate with isopropyl though! | ||
* | **Live z-adjust is called "baby stepping", you will see it on the screen when a print job is running. | ||
* Using the '''0.4mm layer height is recommended'''; it is hitting the max volumetric flow at this setting. Using smaller layer heights will increase time significantly (since the max flowrate is not being reached) and Rana has not tested them. Using the 0.75mm layer height setting may perhaps save about 15-35% time for certain objects. | |||
* Octoprint (must be on lab network): greenmachine.in.hacklab.to, has webcam streaming too! | |||
* No filament runout sensor is installed. But one day it will be !! | |||
</onlyinclude> | </onlyinclude> | ||
* BL-touch flashing red? it is because the little stick at the bottom is not actuating properly because it is being stuck for some reason. To resolve, gently use your finger to pull the stick down and push it back up. Restart the printer, upon start up the BL-touch should go up and down as its start-up test | |||
----- | ----- | ||
== Usage == | |||
=== Running a print job === | |||
* Octoprint is set up. Can also use the USB stick on the side of the touch screen, however for very large gcode files (>3MB?) there can be lag in sending gcode commands to the printer which causes stalling and gaps in the extrustion. For large gcode files use the micro-SD card that is sticking out of the power supply, or use octoprint. | |||
* see next section for configs for PrusaSlicer | |||
* always check the first layer!!! there is live z-adjust on the touchscreen called "baby steps" | |||
* The bed is huge and takes a while to heat up, I suggest setting the bed to heat up before you slice your file (to save time). There is an insulating pad beside the printer you can put on top of the bed to speed up heating. Remove the insulation pad before you run the job or else the nozzle will crash into it!!! | |||
=== Using the touchscreen to command the printer === | |||
* At the home screen, where it shows the nozzle temp and bed temp, fan speed, print speed, etc -> those are buttons you can push to adjust those values (do not have to go through the menu). You can do this while a print job is running to live adjust. | |||
** If you are setting a numerical value, you can click on the numbers and a keypad will pop up to type the number in. E.g. nozzle temperature -> instead of clicking to +10 degrees you can click on the numbers and type something in | |||
** Note: if you adjust a value and then in the gcode there is a command to set that value to something, then the printer will obey the gcode commands it gets. Most relevant for setting the fan speeds since those may be changing at different times in the print job. | |||
* to home the printer: Menu -> Movement -> Home -> Home" | |||
* to move the axis: Menu -> Movement -> Move -> (click the button for the axis/direction you want). The purple button (at the top right) will show the movment increments, push that button to change the increments (cycles through 0.1mm, 1mm, 10mm, 100mm) | |||
=== Loading the filament === | |||
* to load the filament push it all the way through the tubing to the direct drive extruder, then can use the knob on the extruder to load it down to the nozzle. Turn knob clockwise (to the right). | |||
**If you have trouble inserting it into the long tube (ie. it's stuck at the golden push-connect fitting), try to rotate the filament while pushing, or try to clip the end of the filament to a point. | |||
**If all else fail then can remove the tube from the fitting by pushing down on the blue collar and pulling the tubing up. Once the filament has cleared the fitting, insert it into the tubing and re-insert the tubing into the gold fitting. MAKE SURE the tubing is firmly in the fitting or else it will get pulled out and mess up filament feeding. | |||
* to unload, heat up the nozzle and turn the extruder knob counter-clockwise (to the left) | |||
=== Extruder tension for TPU / flexible filaments === | |||
For regular hard plastics, the tensioning knob should be well on with the screw protruding from the knob 2-3mm | |||
For TPU or flexible filaments, it needs to be MORE LOOSE or else the filament could jut out from the space below the extruder gear and above the teflon tube that goes into the heatbreak. It looks pretty funny when the filament shoots out, the filament wants to be free!!!! The knob should be past the screw, with 1-2mm of the knob threads off the screw, it'll look something like this: | |||
[[File: Micro_swiss_extruder_levertension_for_TPU.jpg]] | |||
== Configs == | |||
* to import into prusa slicer: File -> Import -> Import Config Bundle | |||
** to get the physical printer profile make sure to do the bundle on not just "import config"!!! | |||
* on the left panel of prusa slicer, at the top of that panel there should be 3 drop down menus: "Print settings", "Filament" and "Printer". In those menu's select the profiles for the Ender 5 Plus | |||
** BE SURE that the printer profile is set to the ender 5 plus, or else there will be wrong PHYSICAL machine movement limits (In REAL LIFE) and the gcode that is generated will move the printer all weird and could damage the printer!! | |||
* adjust the print settings (add support, or a brim or more perimeters, etc) if desired | |||
* slice it and export the gcode to the usb stick, then plug that into the side of the screen | |||
*When generating the printing file (.gcode file) for '''PETG''', your prusaslicer should look like this in the top right corner! | |||
[[File: E5p_prusa_slicer_usage.JPG]] | |||
'''Unzip these files to get to the .ini file inside! Prusaslicer looks for .ini'''. | |||
Best practise is to delete the previous settings (little "X" beside the preset drop down menu), then load this one | |||
{| cellpadding="5" cellspacing="0" border="1" | {| cellpadding="5" cellspacing="0" border="1" | ||
!Date | !Date | ||
!Filament type | !Name of uploader | ||
!Filament type | |||
! | !Link to config files | ||
!Notes | !Notes | ||
|- | |- | ||
| | | Jan 28, 2025 | ||
| | |Rana | ||
|Config Bundle - Machine Profile and profiles for PETG, PLA, TPU | |||
|[[File:PrusaSlicer_config_bundle_green_machine_with_pysical_printer.zip]] | |||
| | |Has the Green Machine (Ender 5 Plus) machine settings, dialed in settings for elegoo rapid PETG | ||
|- | |- | ||
| | |} | ||
1. | == Tips for printing with a big nozzle == | ||
*The whole point of the big nozzle is to have thicker extrusion lines and bigger layer heights, so less extrusion lines in total are drawn by the printer | |||
*a 0.4mm nozzle will take five extrusion lines to draw 2mm of perimeter, whereas the 1mm nozzle can do it in two lines. 2mm perimeters are pretty freaking strong, you can get away with like infill at 10% or 15% (some people do 5% lol) because most of the strength comes from the perimeters. Just set the top and solid infill to 5 or more layers to make sure it covers up any drooping of the top layers | |||
*So a 1 mm nozzle has a max layer height of 0.75mm. The extrusion width is set to 1.1mm for perimeters and 1.2mm for infill. Upon tuning the settings, was getting max volumetric flow at 0.4mm layer height with no problems, so use that in general. 0.75mm layers does save a bit of time, but looses vertical detail. | |||
*If your part needs to be an exact height, you can try to set the first layer to a value that give the desired final total height (first layer height + 0.75mm*layers = desired height) | |||
*Can also try out prusa slicers cool feature of variable layer height, but never done it who knows what will happen. This should divide the object into vertical sections, which higher detail sections printing at a low layer height, and low detail sections print with a higher layer height | |||
== Hardware == | |||
* 1mm CHT nozzle installed (high flow) | |||
* screen is Big Tree Tech TFT35-E3 V3.0 | |||
* mainboard is Big Tree Tech SKR Mini E3 V3 | |||
**Note: the TMC stepper drivers on the board usually have stealthchop enabled (for silent stepping), however stealthchop fails at speeds above 100mm/s. So for fast travel moves the firmware will switch the stepper drivers to spread cycle mode. So the printer will be louder on fast travel moves. | |||
* power supply is Mean Well RSP-500-24 (the good one, not first release of this printer that had a shitty one) | |||
* Printhead is Micro Swiss Direct Drive and All-Metal Hot end | |||
** https://store.micro-swiss.com/collections/ender-5-plus/products/micro-swiss-direct-drive-extruder-for-creality-ender-5 | |||
* Probe is official BL-Touch (which is stock on the E5P) | |||
** it should be set and forget, don't think it needs to be recalibrated ever unless some hardware thing changes | |||
** can use 'babystep' feature to live z-adjust during printing | |||
** refer to this for setting the probe offset https://www.youtube.com/watch?v=y_1Kg45APko | |||
* Hiwin linear rails on X and Y axis ("good" chinese brand) | |||
* Magnetic spring steel on the print bed, with textured PEI coating | |||
== Direct control of printer == | |||
To use pronterface to control the printer, first power up the printer, then connect the usb cable to your computer. On win10 it should auto-detect and possibly install 'maple' (wtf that is lol). Baud 115200 | |||
== Calibration notes == | |||
* using the built in e-steps I got 137.85 steps/mm (this is in the firmware, in the slicer you just change the flow rate) | |||
* for PLA at 205C, use a max volumetric flow rate of 21 mm^3/s (using 80W heater) | |||
* for TPU at 220C, use a max volumetric flow rate of 10 mm^3/s (using 80W heater) | |||
* for PETG at 235C, use a max volumetric flow rate of 21 mm^3/s (using 80W heater) | |||
== Printable Upgrades == | |||
https://www.thingiverse.com/thing:4742487 | |||
https://www.thingiverse.com/thing:4742501 | |||
Voron cooling fans: https://www.thingiverse.com/thing:5171295 | |||
Z-axis sync indicators: https://www.thingiverse.com/thing:4460521 | |||
== | == Print bed usage == | ||
The stock glass plate with magnetic backing has been put on upside down and taped to the heat bed via Kapton tape. The removeable PEI spring sheet is then stuck on that magnetic sheet. | |||
Wait for the PEI sheet to cool before removing your prints, take it off the bed and it will cool faster. PETG can rip off the PEI coating if it too hot. | |||
Advisable to set the bed temperature to 10 degree's hotter than usual, because the heat has to go through the glass sheet to the PEI sheet. The +10 degrees are already incorporated into the print settings uploaded here. | |||
There is an insulating sheet on the left side of the printer. Use it to speed up the bed pre-heating. | |||
== SD Card == | == SD Card == | ||
Line 101: | Line 142: | ||
==Slicer Settings== | ==Slicer Settings== | ||
Use the config bundle for prusa slicer, a copy is in this wiki under 'usage' and another copy is on the USB drive. | |||
Keep in mind that this printer has a 1mm nozzle installed. So for an object with 1 perimeter is the equivalent of 2.5 perimeters with a 0.4 nozzle (so decently strong). So for most objects 2 perimeters and 4 top/bottom layers is plenty of plastic and will be strong enough. This will save a shitload of time!! | |||
==A few random printing tips== | ==A few random printing tips== | ||
*just pray to the right god lol | |||
*there is a big bed on this printer that takes like 10 min to heat up, so it could be wise to set the bed to heat with inuslating pad while you slice your file | |||
==Octoprint at octopi4.hacklab.to== | ==Octoprint at octopi4.hacklab.to== | ||
Line 129: | Line 173: | ||
|- | |- | ||
| Nov 1, 2023 | |||
| 1mm nozzle installed and it works!!! | |||
| Rana | |||
|- | |||
| Spring 2024 | |||
| Linear rails installed, copper alloy heatblock with 80W heater cartridge installed. Texture PEI spring sheet installed. | |||
| Rana | |||
|- | |||
| Summer 2024 | |||
| Marlin 2.1 installed as firmware, linear advance setting tuned for PETG, PLA and TPU. Acceleration and jerk settings tuned. Speed and retraction settings dailed in for 0.4mm layer heights. | |||
| Rana | |||
|- | |||
Latest revision as of 21:21, 11 April 2025
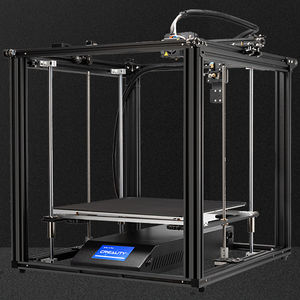
Status
- Working - Read wiki instructions before use
- You must download the configs in the "Config" section below.
- The printer should be "set and forget", the touch probe and the bed mesh should give perfect first layers everytime. Still wipe the build plate with isopropyl though!
- Live z-adjust is called "baby stepping", you will see it on the screen when a print job is running.
- Using the 0.4mm layer height is recommended; it is hitting the max volumetric flow at this setting. Using smaller layer heights will increase time significantly (since the max flowrate is not being reached) and Rana has not tested them. Using the 0.75mm layer height setting may perhaps save about 15-35% time for certain objects.
- Octoprint (must be on lab network): greenmachine.in.hacklab.to, has webcam streaming too!
- No filament runout sensor is installed. But one day it will be !!
- BL-touch flashing red? it is because the little stick at the bottom is not actuating properly because it is being stuck for some reason. To resolve, gently use your finger to pull the stick down and push it back up. Restart the printer, upon start up the BL-touch should go up and down as its start-up test
Usage
Running a print job
- Octoprint is set up. Can also use the USB stick on the side of the touch screen, however for very large gcode files (>3MB?) there can be lag in sending gcode commands to the printer which causes stalling and gaps in the extrustion. For large gcode files use the micro-SD card that is sticking out of the power supply, or use octoprint.
- see next section for configs for PrusaSlicer
- always check the first layer!!! there is live z-adjust on the touchscreen called "baby steps"
- The bed is huge and takes a while to heat up, I suggest setting the bed to heat up before you slice your file (to save time). There is an insulating pad beside the printer you can put on top of the bed to speed up heating. Remove the insulation pad before you run the job or else the nozzle will crash into it!!!
Using the touchscreen to command the printer
- At the home screen, where it shows the nozzle temp and bed temp, fan speed, print speed, etc -> those are buttons you can push to adjust those values (do not have to go through the menu). You can do this while a print job is running to live adjust.
- If you are setting a numerical value, you can click on the numbers and a keypad will pop up to type the number in. E.g. nozzle temperature -> instead of clicking to +10 degrees you can click on the numbers and type something in
- Note: if you adjust a value and then in the gcode there is a command to set that value to something, then the printer will obey the gcode commands it gets. Most relevant for setting the fan speeds since those may be changing at different times in the print job.
- to home the printer: Menu -> Movement -> Home -> Home"
- to move the axis: Menu -> Movement -> Move -> (click the button for the axis/direction you want). The purple button (at the top right) will show the movment increments, push that button to change the increments (cycles through 0.1mm, 1mm, 10mm, 100mm)
Loading the filament
- to load the filament push it all the way through the tubing to the direct drive extruder, then can use the knob on the extruder to load it down to the nozzle. Turn knob clockwise (to the right).
- If you have trouble inserting it into the long tube (ie. it's stuck at the golden push-connect fitting), try to rotate the filament while pushing, or try to clip the end of the filament to a point.
- If all else fail then can remove the tube from the fitting by pushing down on the blue collar and pulling the tubing up. Once the filament has cleared the fitting, insert it into the tubing and re-insert the tubing into the gold fitting. MAKE SURE the tubing is firmly in the fitting or else it will get pulled out and mess up filament feeding.
- to unload, heat up the nozzle and turn the extruder knob counter-clockwise (to the left)
Extruder tension for TPU / flexible filaments
For regular hard plastics, the tensioning knob should be well on with the screw protruding from the knob 2-3mm For TPU or flexible filaments, it needs to be MORE LOOSE or else the filament could jut out from the space below the extruder gear and above the teflon tube that goes into the heatbreak. It looks pretty funny when the filament shoots out, the filament wants to be free!!!! The knob should be past the screw, with 1-2mm of the knob threads off the screw, it'll look something like this:
Configs
- to import into prusa slicer: File -> Import -> Import Config Bundle
- to get the physical printer profile make sure to do the bundle on not just "import config"!!!
- on the left panel of prusa slicer, at the top of that panel there should be 3 drop down menus: "Print settings", "Filament" and "Printer". In those menu's select the profiles for the Ender 5 Plus
- BE SURE that the printer profile is set to the ender 5 plus, or else there will be wrong PHYSICAL machine movement limits (In REAL LIFE) and the gcode that is generated will move the printer all weird and could damage the printer!!
- adjust the print settings (add support, or a brim or more perimeters, etc) if desired
- slice it and export the gcode to the usb stick, then plug that into the side of the screen
- When generating the printing file (.gcode file) for PETG, your prusaslicer should look like this in the top right corner!
Unzip these files to get to the .ini file inside! Prusaslicer looks for .ini. Best practise is to delete the previous settings (little "X" beside the preset drop down menu), then load this one
Date | Name of uploader | Filament type | Link to config files | Notes |
---|---|---|---|---|
Jan 28, 2025 | Rana | Config Bundle - Machine Profile and profiles for PETG, PLA, TPU | File:PrusaSlicer config bundle green machine with pysical printer.zip | Has the Green Machine (Ender 5 Plus) machine settings, dialed in settings for elegoo rapid PETG |
Tips for printing with a big nozzle
- The whole point of the big nozzle is to have thicker extrusion lines and bigger layer heights, so less extrusion lines in total are drawn by the printer
- a 0.4mm nozzle will take five extrusion lines to draw 2mm of perimeter, whereas the 1mm nozzle can do it in two lines. 2mm perimeters are pretty freaking strong, you can get away with like infill at 10% or 15% (some people do 5% lol) because most of the strength comes from the perimeters. Just set the top and solid infill to 5 or more layers to make sure it covers up any drooping of the top layers
- So a 1 mm nozzle has a max layer height of 0.75mm. The extrusion width is set to 1.1mm for perimeters and 1.2mm for infill. Upon tuning the settings, was getting max volumetric flow at 0.4mm layer height with no problems, so use that in general. 0.75mm layers does save a bit of time, but looses vertical detail.
- If your part needs to be an exact height, you can try to set the first layer to a value that give the desired final total height (first layer height + 0.75mm*layers = desired height)
- Can also try out prusa slicers cool feature of variable layer height, but never done it who knows what will happen. This should divide the object into vertical sections, which higher detail sections printing at a low layer height, and low detail sections print with a higher layer height
Hardware
- 1mm CHT nozzle installed (high flow)
- screen is Big Tree Tech TFT35-E3 V3.0
- mainboard is Big Tree Tech SKR Mini E3 V3
- Note: the TMC stepper drivers on the board usually have stealthchop enabled (for silent stepping), however stealthchop fails at speeds above 100mm/s. So for fast travel moves the firmware will switch the stepper drivers to spread cycle mode. So the printer will be louder on fast travel moves.
- power supply is Mean Well RSP-500-24 (the good one, not first release of this printer that had a shitty one)
- Printhead is Micro Swiss Direct Drive and All-Metal Hot end
- Probe is official BL-Touch (which is stock on the E5P)
- it should be set and forget, don't think it needs to be recalibrated ever unless some hardware thing changes
- can use 'babystep' feature to live z-adjust during printing
- refer to this for setting the probe offset https://www.youtube.com/watch?v=y_1Kg45APko
- Hiwin linear rails on X and Y axis ("good" chinese brand)
- Magnetic spring steel on the print bed, with textured PEI coating
Direct control of printer
To use pronterface to control the printer, first power up the printer, then connect the usb cable to your computer. On win10 it should auto-detect and possibly install 'maple' (wtf that is lol). Baud 115200
Calibration notes
- using the built in e-steps I got 137.85 steps/mm (this is in the firmware, in the slicer you just change the flow rate)
- for PLA at 205C, use a max volumetric flow rate of 21 mm^3/s (using 80W heater)
- for TPU at 220C, use a max volumetric flow rate of 10 mm^3/s (using 80W heater)
- for PETG at 235C, use a max volumetric flow rate of 21 mm^3/s (using 80W heater)
Printable Upgrades
https://www.thingiverse.com/thing:4742487 https://www.thingiverse.com/thing:4742501
Voron cooling fans: https://www.thingiverse.com/thing:5171295
Z-axis sync indicators: https://www.thingiverse.com/thing:4460521
Print bed usage
The stock glass plate with magnetic backing has been put on upside down and taped to the heat bed via Kapton tape. The removeable PEI spring sheet is then stuck on that magnetic sheet.
Wait for the PEI sheet to cool before removing your prints, take it off the bed and it will cool faster. PETG can rip off the PEI coating if it too hot.
Advisable to set the bed temperature to 10 degree's hotter than usual, because the heat has to go through the glass sheet to the PEI sheet. The +10 degrees are already incorporated into the print settings uploaded here.
There is an insulating sheet on the left side of the printer. Use it to speed up the bed pre-heating.
SD Card
Slicer Settings
Use the config bundle for prusa slicer, a copy is in this wiki under 'usage' and another copy is on the USB drive.
Keep in mind that this printer has a 1mm nozzle installed. So for an object with 1 perimeter is the equivalent of 2.5 perimeters with a 0.4 nozzle (so decently strong). So for most objects 2 perimeters and 4 top/bottom layers is plenty of plastic and will be strong enough. This will save a shitload of time!!
A few random printing tips
- just pray to the right god lol
- there is a big bed on this printer that takes like 10 min to heat up, so it could be wise to set the bed to heat with inuslating pad while you slice your file
Octoprint at octopi4.hacklab.to
I wish...
Maintenance Resources
put stuff here lol
Maintenance Log
Most recent entries at the top.
Date | Notes | Entry By |
---|---|---|
June 9, 2022 | Setting up the printer | Rana |
Nov 1, 2023 | 1mm nozzle installed and it works!!! | Rana |
Spring 2024 | Linear rails installed, copper alloy heatblock with 80W heater cartridge installed. Texture PEI spring sheet installed. | Rana |
Summer 2024 | Marlin 2.1 installed as firmware, linear advance setting tuned for PETG, PLA and TPU. Acceleration and jerk settings tuned. Speed and retraction settings dailed in for 0.4mm layer heights. | Rana |