Discov3ry Paste Extruder: Difference between revisions
(Created page with "So a hacklab member (me, tdmckee Trevor) supported the Discov3ry Paste Extruder on Kickstarter, and just recently received it. Its currently in the lab, attached to the [...") |
No edit summary |
||
(11 intermediate revisions by one other user not shown) | |||
Line 1: | Line 1: | ||
So a hacklab member (me, [[ | |||
So a hacklab member (me, [[User:Tdmckee]]) supported the Discov3ry Paste Extruder on Kickstarter (#304!), and just recently received it. Its currently in the lab, attached to the [[Makerbot]]. Here's a [[https://twitter.com/tdmckee/status/626242147960942593 tweet with a picture.]] | |||
We were initially having some issues with getting extrusion to work (as documented below in troubleshooting), but it all turned out to revolve around the fact that the printer firmware would interrupt if it didn't read an extrusion temperature (because we had disconnected the extruder thermocouple along with the other filament extruder parts). Plugging the thermocouple back in, and removing some limits associated with extrusion speed (due to high gear ratios between the paste extrusion stepper motor and the actual plunger), we were finally able to [[https://youtu.be/HQPGpnGQW0Y successfully extrude a blob of acrylic painters caulk]] (our test paste) onto the [[Makerbot]] bed! | |||
[[File:First_demo_paste_extruder_print_2015-08-09_09-15.jpg|thumbnail|First demo paste extruder print]] | |||
---- | |||
== Troubleshooting == | |||
* Were experiencing a MINTEMP error. | |||
** Manually adding M302 (enable cold extrusion) into the start gcode in CURA, | |||
** Commenting out / removing any M109 set temperature commands, and | |||
** Plugging in an extruder thermocouple to read out _some_ temperature (as would otherwise encounter a MINTEMP error, code 0, preventing the print from starting). Had Asked the [[http://forum.structur3d.io/ structur3d.io forum]], received [[http://forum.structur3d.io/t/enabling-cold-extrusion-avoiding-mintemp-erroe/321 this reply]]... Need to update the forum with our methods to overcome the error. | |||
* Extrusion speed needs modification | |||
** [[http://forum.structur3d.io/t/um2-wiring-advice-gcode-modification-using-cura/303 here's another structur3d forum post]] with some other recommended settings for enabling cold extrusion, along with changing extrusion feed rates. | |||
** removed some extrusion step multipliers from the extrusion hardware, such that sending code "G1 F18000 E270" via pronterface would pretty much result in one full rotation of the large white gear underneath the extruder. | |||
** Need to determine how much volume that equates to coming out of the 50ml syringe, and adjust feed settings appropriately to extrude proper amounts. We were definitely experiencing some delay / leaky extrusion following a period of extrusion from the syringe, may be due to high pressures required to force viscous paste through the extruder, and /or perhaps bulging of the tubing with a step increase in pressure, which may cause more extrusion down the line. | |||
== Stuff to extrude == | |||
Apparently structur3d have a list with some settings to try (though hopefully somewhere more organized than that forum, which seems a little free-for-all unstructured) | |||
My list: | |||
* Silicone Caulk | |||
* Wood Filler | |||
* Various edible things | |||
* ... other? Happy to field suggestions... | |||
== To Dos == | |||
Some plans / to dos for the future: | |||
* Insert some sort of pressure sensor / transducer in line with the extruder, to monitor changes in pressure in the lines, and maybe figure out if there's any weird viscoelastic coupling we need to be dealing with with regards to the delay in between extrusion pumo going and stuff coming out the extrusion nozzle. May require some fancy extruder retraction code if there's a complex temporal relationship between extrusion, pressure in the syringe, and pressure in the line/nozzle... | |||
* Figure out appropriate feed rates | |||
* maybe figure out a less viscous test material - had to press pretty vigorously on the syringe to force the caulk through the lines... | |||
* ... | |||
== Pictures! == | |||
Pictures and a video of the setup are available at [[https://www.flickr.com/gp/tdmckee/1oCv88 this flickr album]] | |||
[[Category:Equipment]] |
Latest revision as of 07:22, 16 January 2019
So a hacklab member (me, User:Tdmckee) supported the Discov3ry Paste Extruder on Kickstarter (#304!), and just recently received it. Its currently in the lab, attached to the Makerbot. Here's a [tweet with a picture.]
We were initially having some issues with getting extrusion to work (as documented below in troubleshooting), but it all turned out to revolve around the fact that the printer firmware would interrupt if it didn't read an extrusion temperature (because we had disconnected the extruder thermocouple along with the other filament extruder parts). Plugging the thermocouple back in, and removing some limits associated with extrusion speed (due to high gear ratios between the paste extrusion stepper motor and the actual plunger), we were finally able to [successfully extrude a blob of acrylic painters caulk] (our test paste) onto the Makerbot bed!
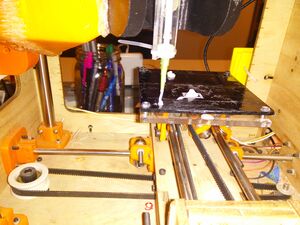
Troubleshooting
- Were experiencing a MINTEMP error.
- Manually adding M302 (enable cold extrusion) into the start gcode in CURA,
- Commenting out / removing any M109 set temperature commands, and
- Plugging in an extruder thermocouple to read out _some_ temperature (as would otherwise encounter a MINTEMP error, code 0, preventing the print from starting). Had Asked the [structur3d.io forum], received [this reply]... Need to update the forum with our methods to overcome the error.
- Extrusion speed needs modification
- [here's another structur3d forum post] with some other recommended settings for enabling cold extrusion, along with changing extrusion feed rates.
- removed some extrusion step multipliers from the extrusion hardware, such that sending code "G1 F18000 E270" via pronterface would pretty much result in one full rotation of the large white gear underneath the extruder.
- Need to determine how much volume that equates to coming out of the 50ml syringe, and adjust feed settings appropriately to extrude proper amounts. We were definitely experiencing some delay / leaky extrusion following a period of extrusion from the syringe, may be due to high pressures required to force viscous paste through the extruder, and /or perhaps bulging of the tubing with a step increase in pressure, which may cause more extrusion down the line.
Stuff to extrude
Apparently structur3d have a list with some settings to try (though hopefully somewhere more organized than that forum, which seems a little free-for-all unstructured)
My list:
- Silicone Caulk
- Wood Filler
- Various edible things
- ... other? Happy to field suggestions...
To Dos
Some plans / to dos for the future:
- Insert some sort of pressure sensor / transducer in line with the extruder, to monitor changes in pressure in the lines, and maybe figure out if there's any weird viscoelastic coupling we need to be dealing with with regards to the delay in between extrusion pumo going and stuff coming out the extrusion nozzle. May require some fancy extruder retraction code if there's a complex temporal relationship between extrusion, pressure in the syringe, and pressure in the line/nozzle...
- Figure out appropriate feed rates
- maybe figure out a less viscous test material - had to press pretty vigorously on the syringe to force the caulk through the lines...
- ...
Pictures!
Pictures and a video of the setup are available at [this flickr album]